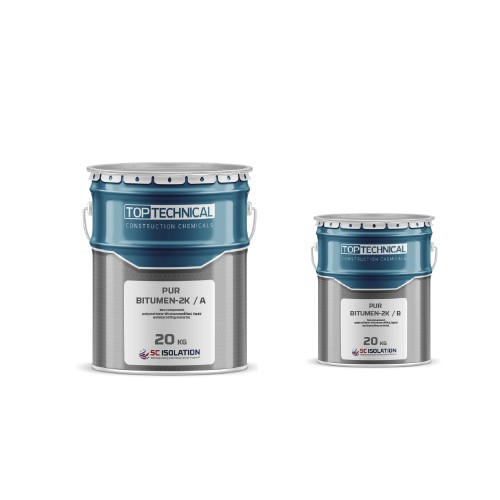
DESCRIPTION
PUR BITUMEN 2K is a two component, polyurethane-bitumen modified, liquid waterproofing material. It is a fast curing product and it forms a very elastic film, which perfectly adhere to different surfaces. It is perfectly adhesive to almost all types of surfaces. It has excellent mechanical characteristics providing high tension, tearing and wearing resistance. It has excellent chemical resistance. Moreover, does not affected by water vapor transmission. The dry film of the product has the capability to breath and prevents the accumulation of humidity under the coat. It provides thick coating without bubbling. It provides high crack bridging. It has excellent covering and is adhesive to surface. It has high thermal resistance and can be used between +80°C and 200 °C. The film applied keeps its flexibility down to – 40 °C.
AREA OF USES
- Roof and terrace areas
- Parking lots
- Aircraft hangars
- Tunnels
- Asphalt and EPDM membranes
- Planting pot and green roof systems
- Insulation of roofs made of metal and fibrous cement
- Utility water tanks
- Insulation of foundation and shear concretes of constructions
- Irrigation channels
ADVANTAGES
- Mixing process is easy as the components are in 1/1 by volume.
- It is fast curing product.
- It provides thick coating, no bubbling.
- It has excellent crack bridging.
- It is highly adhesive to almost all types of surfaces, coated or uncoated.
- Thanks to its excellent thermal resistance, the product never becomes soft. Its maximum usage temperature is 80 °C, while the maximum shock temperature is 200 °C.
- The product have very good resistance to cold weather, the film keeps its elasticity up to -40°C.
- It has excellent mechanical characteristics providing high elongation, tension, tearing and wearing resistance.
- It is highly resistant to chemicals.
- It is effective as water vapor barrier.
SHELF LIFE / STORAGE CONDITIONS
24 months from date of production.
The product must be stored as per local storage regulations and should be kept in dry and well-ventilated location far from heat and direct sunlight.
AVAILABILITY
Available in 30 kg (Metal can)
(Packing may vary from country to country depending on local requirements)
PHYSICAL CONSTANTS
Shade / Colors | : Dark Brownish black liquid |
Finish | : High Gloss |
Theoretical spreading | : 1 m²/ litre (600 micron DFT) |
Recommended DFT | : 600 - 800 micron for horizon surfaces / 200 - 400 microns for vertical surfaces |
Elongation to break | : 24 hour(s) 20°C / 68°F |
Density | : 72 hours (20°C / 68°F) |
Pot Life | : 20-30 minutes |
Tension Strength at Break (N/mm2) | : >2 (DIN 53504) |
Hardness (Shore A) | : 35 (ASTM D2240 / DIN 53505 / ISO R868) |
Tearing Resistance (N/mm²) | : 20-22 |
Service Temperature | : -40 to +80 º C |
Surface dry | : 1 approx. hour(s) 20°C/68°F |
Dry to touch | : 8 hour(s) 20°C/68°F |
Hard Dry | : 24 hour(s) 20°C/68°F |
Recoat interval, min. | : 24 hour(s) 20°C/68°F |
APPLICATION DETAILS
Application method | : Airless spray / Brush and roll / Metal Trowel |
Thinner | : Do Not thin the product. |
Mixing Ratio | : 1 (by volume) |
SURFACE PREPARATION
For Concrete surfaces: All surfaces (new or old) must be clean, dry and free from grease and oil, laitance, curing compounds, form board release agents and any other contaminants which may impair adhesion of the product. Remove any residual paint with paint stripper, scraping, grinding and/or sand blasting to achieve a clean surface , for new concrete surfaces must have “cured” for at least 28 days and should be porous, and of a light broom finish to ensure maximum adhesion between base coat and concrete. Diamond disk grinding is necessary and use the surface should be sealed with suitable primer as follow:
If the Humidity Rate ≤ 4% use T.T SF Epoxy Sealer.
If the Humidity Rate 4% - 12% Use T.T SF-MT Epoxy Sealer.
PRECEDING COAT
- T.T SF Epoxy Sealer for dry concrete surfaces
- T.T SF-MT Epoxy Sealer for concrete surfaces that have humidity above 8%. For Wood Surfaces use T.T PU FLEX PRIMER-2K
- For PVC Surfaces use T.T PUR-PRIMER-1K
- For bitumen Coated surface Use T.T PU flex Primer -2K
APPLICATION CONDITIONS
Component A and B of the product are given in separate packages with their mixture rates. Component B is poured into component A and stirred with a hand mixer in 300 rev/min. Material has to be used immediately after mixing process. Product’s container life is 20-25 minutes in 20 °C. The mixture is applied to the prepared surface by using a roller, brush or spatula. Please ensure that the floor temperature is above 10°C during the application process. Different coatings should be used for shiny surfaces, metal and aluminum surfaces. Please ensure that applied surfaces are protected (direct contact with water) for minimum 24 hours. Minimum consumption is in between 1,0 and 1,6 lt/m2 depending on the application surface.
SAFETY
Handle with care. Before and during use, observe all safety labels on packaging and paint containers, consult T.T material safety data sheets and follow all local or national safety regulations. Avoid inhalation, avoid contact with skin and eyes and do not swallow. Take precautions against possible risks of fire or explosions as well as protection of the environment. Apply only in well-ventilated areas.
REMARK
- All technical data stated in this Product Data Sheet are based on laboratory tests. Actual values may vary due to circumstances beyond our controls.
- Newly applied material should not be exposed to rain and frost for 24 hours.
- Thickness should be at least 1mm in applications that will be exposed to sunlight.
- It should not be used in rainy and fog weather under + 5 ° C.