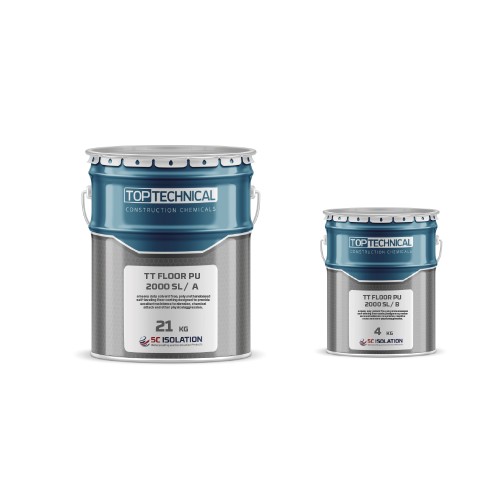
Floor PU 2000 SL is a heavy duty solvent free, polyurethane based self-levelling floor coating designed to provide excellent resistance to abrasion, chemical attack and other physical aggression
AREA OF USES
- Durable and hard wearing
- Very good abrasion and chemical resistance
- Solvent free – no odour during application
- Self-levelling, easy to apply
- Flexible, semi-elastic
- Crack bridging
SUBSTRATES
Concrete, wood, metal floors.
SHELF LIFE / STORAGE CONDITIONS
24 months from date of production.
The product must be stored as per local storage regulations and should be kept in dry and well-ventilated location far from heat and direct sunlight.
AVAILABILITY
Available in 25 kg as set (Metal cans)
(Packing may vary from country to country depending on local requirements)
PHYSICAL CONSTANTS
Shade /Colours | : Grey, light grey, red, green, blue. (Further colours are available on request) |
Finish | : High Gloss |
Volume solids % | : 100 % |
Theoretical spreading | : 0.5 m²/ litre (2 mm dry film thickness) |
Recommended DFT | : 1500 – 2500 micron (1,5 – 2,5 mm) |
Flash point | : 130 ° C / 266 °F |
VOC | : 12 g/ltr |
Specific gravity | : 1,45 ± 0.01 kg/litre |
Elongation | : Up to 40% (ASTM D412) |
Tensile Strength | : 25 N/mm2 (ASTM D412) |
Tear Strength | : >40 N/mm2 (ASTM D624) |
Compressive Strength | : 50 N/mm2 (ASTM C 579) |
Adhesion Strength | : >2.5 N/mm2 |
Shore D Hardness | : 75 |
Surface dry | : 6 approx. hour(s) 20°C/68°F |
Dry to touch | : 12 - 18 hour(s) 20°C/68°F |
Hard Dry | : 24 hour(s) 20°C/68°F |
Fully cured | : 7 days 20°C/68°F |
APPLICATION DETAILS
Mixing Ratio | : 21 Component A : 3 Component B (by weight) |
Permissible ambient and substrate temperature | : +8°C - (+) 30°C |
Application method | : Airless spray / Brush and roll / Metal Trowel |
Thinner | : Do Not thin the product. |
Pot life | : >30 min approx. hour(s) 20°C/68°F (Working time for epoxy systems decreases when ambient temperature rises.) |
SURFACE PREPARATION
The surface of the concrete to be prepared shall be sound, clean and uncontaminated. This preparation shall be such as to leave a sound exposed concrete surface free from dust, loose particles and any deleterious matter. If the concrete surface is defective or has laitance, it must be cut back to a sound base. Excess laitance deposits are best removed by light mechanical scrabbling, grinding or grit/captive blasting followed by vacuum cleaning to remove dust debris. Any blowholes, chipping or similar surface imperfections shall be repaired using, a solvent free epoxy resin repair mortar. Expansion joints shall be repaired using, a high strength solvent free epoxy mortar.
New concrete or cementitious surfaces should be allowed to cure and have moisture content not exceeding 5%. Old or existing floor should be refurbished mechanically to ensure clear sound substrate.
PRIMING
Highly porous concrete or concrete containing micro-silica must be treated with Epoxy or polyurethane. The primer should be applied by brush or roller on to the cleaned surface area (particularly hidden surfaces). The primer should be left to achieve a tack-free condition for 6-8 hours before applying the top coat. A second coat of primer may be required if the substrate is excessively porous.
Metal surface must be perfectly cleaned up to white metal by sand blasting, and then treated with one coat of Epoxy or polyurethane before the oxidation process begins again.
PRECEDING COAT
SF Epoxy Sealer, or T.T Epoxy Sealer SF-MT, PU FLEX PRIMER 2K.
MIXING
The product is supplied in two pre-weighed packs (Component A – Base and Component B – Hardener) which are ready for immediate in-site use.
Pre-condition the Components A and B to a temperature of approximately 15- 25°C before mixing.
The contents of the base container should be mixed for 1-2 minutes with a proprietary paddled drill.
Transfer the entire content of Component B into the Container A and mix for further 2-3 minutes without causing air bubbles until a homogeneous mix is-obtained.
APPLICATION
Pour the mixed material unto the primed surface in pools or as large strip. Spread the material evenly to the desired thickness using a notch trowel. Continuous spiking with a spiked roller is to be done.
APPLICATION CONDITIONS
Use only where application and drying can proceed at temperatures above 5°C, and relative humidity is below 75%. Apply only on a dry and clean surface.
RECOMMENDATIONS
- The curing time of the product is influenced by the ambient, material and ambient temperatures.
- At high temperatures, chemical reactions are speeding up thus shortens the pot life, open time and the curing times.
- The product should not be applied on surfaces with a risk of rising dampness.
- Do not mix more material than can be used within the pot life of mixture.
- Incorrect assessment treatment of cracks may lead to a reduced service life and reflective cracking.
SAFETY
Handle with care. Before and during use, observe all safety labels on packaging and paint containers, consult T.T material safety data sheets and follow all local or national safety regulations. Avoid inhalation, avoid contact with skin and eyes and do not swallow. Take precautions against possible risks of fire or explosions as well as protection of the environment. Apply only in well-ventilated areas.