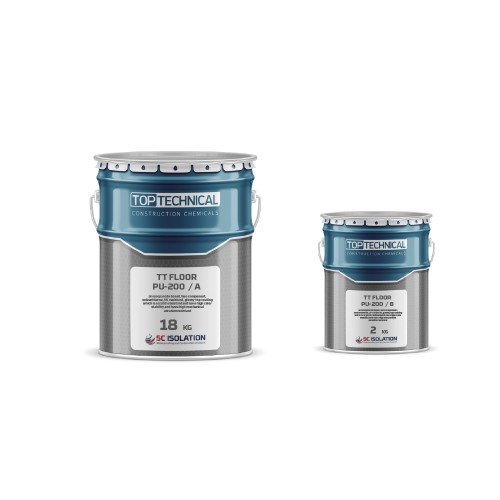
T.T Floor PU 200 is an isocyanate based, two component, solvent borne, UV resistant, glossy top coating which is scratch resistant and have high colour stability and have high mechanical abrasion resistant.
AREA OF USES
- Indoor and outdoor application.
- Horizontal and vertical applications.
- It can be used on concrete, steel and wooden surfaces.
- As a topcoat in places open to atmospheric conditions where high UV resistance, colour stability and glossiness is required.
- As protection over epoxy systems for outdoor uses.
SUBSTRATES
Concrete, wood, metal floors.
ADVANTAGES OF THE PRODUCT
- The product is none yellowing and UV resistance.
- The product have high resistant to atmospheric conditions.
- The product have very good gloss retention.
- The product have very good scratch resistance.
- The product have very good resistance to salt water, solutions with salts, diluted weak acids, gasoline and mineral oils.
- Easy to apply with an airless spray gun or roller.
- Easy to clean thanks to its smooth surface.
SHELF LIFE / STORAGE CONDITIONS
24 months from date of production.
The product must be stored as per local storage regulations and should be kept in dry and well-ventilated location far from heat and direct sunlight.
AVAILABILITY
Available in 20 kg 5 kg as set (Metal cans)
(Packing may vary from country to country depending on local requirements)
PHYSICAL CONSTANTS
Shade / Colors | : RAL colour Card |
Finish | : High Gloss |
Volume solids % | : 65% |
Theoretical spreading | : 8.67 m²/litre (75 Micron DFT) |
Recommended DFT | : 100-200 micron |
Mixture Density | : 1.2 ± 0.05 kg/L (Changes depending on the colour) |
Bond Strength by Pull- off | : > 2 N/mm2 (EN 1504-2) 7 days |
Abrasion Resistance (Taber) | : 75 mg, 1000 cycle (EN 1504-2) |
Specific gravity | : 1,45 ± 0.01 kg/litre |
Impact Resistance | : Class III (EN 1504-2) |
Flash Point | : > 21°C |
Pot Life | : 4 - 6 hours (23°C) |
Application Temperature | : Between +10°C and +30°C |
Dry to touch | : 2 - 4 hour(s) 20°C/68°F |
Recoating interval | : 24 hour (s) 20°C/68°F |
Hard Dry | : 8 - 10 hour(s) 20°C/68°F |
Fully cured | : 7 days 20°C/68°F |
APPLICATION DETAILS
Mixing Ratio | : Component A : 9 Component 1 (by weight) |
Thinner | : 10 % for roller application – 5 % for airless spray – 25 % for air spray |
Pot life | : > 40 min approx. hour(s) 20°C/68°F |
SURFACE PREPARATION
Please contact 5C ISOLATION technical department for more information about surface preparation according to the surface you are painting.
PRECEDING COAT
Contact Technical department for Primer to be used according to the surface you are painting.
COLORS/COLOR STABILITY
Colour stability for some shades may be effected by exposure to harsh chemical atmospheres. This does not affect the performance of the coating. For certain colours, extra coats may be necessary to obtain full opacity.
CURING AGENT
The curing agent of the product is sensitive to moisture. Even small traces of water in the mixed paint will reduce the pot life and result in film defects. Open curing agent cans with caution as overpressure might exist. Store in a dry place and keep the can tightly closed until use.
MIXING
The product is supplied in two pre-weighed packs (Component A – Base and Component B – Hardener) which are ready for immediate in-site use.
Pre-condition the Components A and B to a temperature of approximately 15- 25°C before mixing.
The contents of the base container should be mixed for 1-2 minutes with a proprietary paddled drill.
Transfer the entire content of Component B into the Container A and mix for further 2-3 minutes without causing air bubbles until a homogeneous mix is obtained.
FOR ANTI SLIP SURFACE
For anti-slip surfaces, fine sand must be spread on the top of the paint while it is still wet. The surface is allowed to cure for at least 24 hours; the excess aggregate should be vacuum cleaned from the surface then apply a 2nd coat with a medium texture roller of T.T Epoxy Top coat SF. Care should be taken to ensure that continuous film is achieved and all grains are completely covered and coated by the epoxy mixture. The optional slip resistant texture is provided by the range of the coarse sand selected
APPLICATION CONDITIONS
Use only where application and drying can proceed at temperatures above 5°C, and relative humidity is below 75%. Apply only on a dry and clean surface.
RECOMMENDATIONS
- The curing time of the product is influenced by the ambient, material and ambient temperatures.
- At high temperatures, chemical reactions are speeding up thus shortens the pot life, open time and the curing times.
SAFETY
For information and advice on the safe handling, storage and disposal of chemical products, users should refer to the most recent Material Safety Data.
Sheet containing physical, ecological, toxicological and other safety-related data.
REMARK
- All technical data stated in this Product Data Sheet are based on laboratory tests. Actual values may vary due to circumstances beyond our controls.
- Newly applied material should not be exposed to water and frost for 24 hours. It should not be used in rainy and fog weather under + 5 ° C